

Chances are oh, astronomically small that your owners manual or parts list has these Movement on the bearings*, take these measurements. If you’re simply changingīearings due to mild problems and there is no obvious sign of axial arbor (as in my case) the whole assembly is so worn/shot that these measurementsĪre probably not reliable to begin with. These measurements will need to be duplicated during re-assembly UNLESS
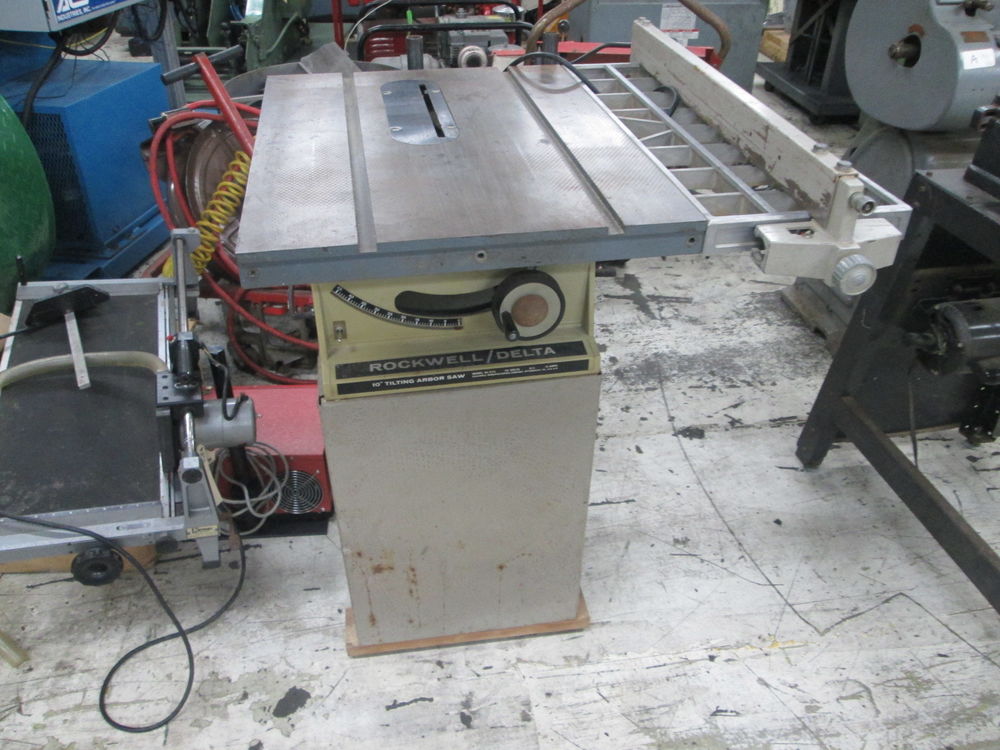
Your saw may or may not need access to these flats. However my saw does not make use of these flats, therefore the flange is pushed flush to the ID of the bearing, which means the flats are then inaccessible. NOTE: My flange was a "universal" flange used by Rockwell which has flats on the bearing side of the flange. If you need to fit a spanner wrench in there, make a measurement. This may depend on whether changing blades on your saw requires a spanner wrench to be inserted on the non-blade side of the flange - the flange may have flats. Distance from any point on the flange to a point on the cast housing.Īlso, check to see if the small part of the flange butts up against the ID of the bearing.Distance from any point on the pulley to a point on the cast housing.Length of arbor from the end (pulley side) to a point on the cast.To take the following measurements (refer to diagrams): When this happens on the ID of the bearing, the bearing itself can literally "eat" right through the arbor (called fretting corrosion) and actually cut it in half! I doubt this is a real concern in a tablesaw as drastically poor performance would show up long before the arbor gave way (which describes my case).īefore you begin disassembly of the arbor and bearings, it’s a good idea Is that one press fit will loosen over time more than the other - thisīegins a cycle whereby the one "looser" fit begins to "walk" on the mating surface. The second problem will show up over time in just about every suchĪpplication requiring press fits on both bearing surfaces. If both press fits are "tight" you will crush the bearing so that it is difficult or impossible to turn. Inherently there are problems with this design, the first of which is thatĬare must be taken not to "crush" the bearing during assembly. The arbor/bearing assembly depends on "press fits" on both surfaces of the bearing, that is the outside of the bearing itself (the OD) is press fit into a cast housing, and the arbor is press fit on the inside (the ID) of the bearing. This would never allow a straight cut of any kind on this saw. The bearing on the pulley side was "shot". My arbor was badly worn and wiggled side-to-side quite a bit, seemed like The trunnions is grease - that is, both trunnions can slide off if the Thing holding the female section of the trunnions to the male section of Iron top and trunnion assembly come right off. Knock two pins from the crankwheel shafts and the cast Four bolts hold the cast iron top to the base, four more bolts hold the trunnion assembly (trunnions,Ĭast housing for arbor/bearings, worm gears, motor mount plate, etc.) to Other than rusty bolts, this was painless. I also called and spoke with technicians twice they answered each of my questions accurately and with no hesitation. Literally within 30 seconds I was told the saw was made in 1975 and that a parts list and user manual would be sent immediately, no charge.
1951 DELTA ROCKWELL TABLE SAW BUY SERIAL
Obtaining The Paperwork And Creation DateĬalled Delta at 1-80 and gave them the model and serial numbers. It should also be noted the more I take apart and "make like new" the more I take apart the "marginal" stuff, then the stuff that looked good to begin with starts to look bad. Saw was basically useless as is, but the price was right. However the cast iron tabletop and all steel items were badly rusted (although structurally sound) and the arbor had about 1/8"+ play side-to-side. The mobile base was in good shape, as were the wheel cranks. I acquired an old 10" Rockwell Contractors Saw and wished to make it "run and look like new". This model was the precursor to the current delta 34-444 and I'd imagine most of the items discussed are relevant to similar contractor-style saws. This document covers my repair-rebuild of a Rockwell tablesaw, model 34-348.
